Informing and educating the advanced materials and process engineering community.
Each conference category includes a variety of programs that inform and educate materials and processes professionals, including engineers, product managers, technicians, sales and marketing personnel.
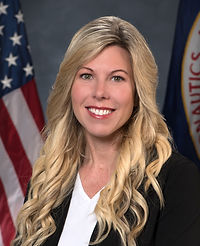
Lindsay Kaldon
Fission Surface Power Project Manager | NASA Glenn Research Center
​
Lindsay Kaldon is the Fission Surface Power Project Manager at NASA’s Glenn Research Center in Cleveland, Ohio. Prior to joining NASA in 2023, she served as the Technical Lead and Deputy Program Manager for the Navy’s Electromagnetic Pulse Office at the Naval Surface Warfare Center in Dahlgren, Virginia. She has over 10 years working in the Department of Defense on unmanned intelligence aircraft for both the Navy and the Air Force. She began her professional career as an Air Force electronic warfare officer on the high-altitude U-2 and Global Hawk aircraft. Lindsay has a Bachelor’s degree in Electrical Engineering from the University of Evansville, a professional certificate in Systems Engineering from the Naval Postgraduate School, and a Master’s degree in Nuclear Engineering from Penn State where her research focused on radioisotope power and nuclear propulsion systems. She is currently a Captain in the Air Force Reserves serving part time within Air Force Research Laboratory’s Space Vehicles Directorate at Kirtland AFB, NM. In her spare time, she enjoys flying; she has a Private Pilot’s License with Instrument Rating.
​
Nuclear Goes to the Moon: Current Status of NASA’s Fission Surface Power Project
Wednesday, May 21, 2025 | 8:00 am – 9:00 am
​
Small nuclear fission systems are powerful and could enable robust space operations for planetary habitation and exploration. On Earth, unless disrupted by storms or grid problems, electrical power for most people is no further than an outlet away. However, the solar system does not provide such easy access to electricity as we know it. Astronauts could take advantage of a reliable power supply to explore both the Moon and Mars. The system will need to be lightweight and capable of running regardless of its location, the weather, or available sunlight and other natural resources. NASA’s Fission Surface Power (FSP) project expands on the efforts of the agency’s Kilopower project, which ended in 2018. Currently, NASA is working with the US Department of Energy and industry to design a fission power system that would provide at least 40 kilowatts of power – enough to continuously run 30 households for ten years. A future lunar demonstration will pave the way for sustainable operations and even base camps on the Moon and Mars.

Ahmed Hassen
Group Leader & Senior R&D Staff Scientist | Oak Ridge National Laboratory (ORNL)
​
Dr. Hassen is the Group Leader for the Composites Innovation (CI) Group in the Manufacturing Science Division (MSD) at Oak Ridge National Laboratory (ORNL). He is leading ORNL's development efforts in high-rate manufacturing of advanced composites structures. Ahmed is leading ORNL’s molds and dies manufacturing portfolio for the composite manufacturing industry. One of his leading efforts is to develop a vision and strategies for smart manufacturing of polymers and advanced composites aiming to advance the U.S. competitiveness in the global market of manufacturing. Dr. Hassen contributed to the creation of a new market for Additive Manufacturing (AM) technologies by developing a new class of composite feedstock materials for large-scale AM systems. He has expertise in a wide variety of composite manufacturing, characterization, and qualification methods and he is currently leading/managing several technical research efforts with a large funding portfolio in this field. Dr. Hassen is mentoring, supporting, and managing a group of undergraduate and graduate students (PhD and Masters), postdoctoral fellows, and junior/senior staffs. Dr. Hassen was serving on the Board of Directors (BOD) of the American Society for Non-destructive Testing (ASNT) and was the Chairman of the ASNT Research Symposium (2020-2022). He has published 90+ articles in high impact journals and proceedings, holds several patents, has received three R&D 100 Awards, named the 2021 Society of Manufacturing Engineers (SME), Jud Hall Composites Manufacturing Award recipient in addition to multiple honors and technical awards.
​

Daniel Coughlin
Senior Staff, Leader of Industrial Collaborations | Oak Ridge National Laboratory (ORNL)
​
Dan has more than 30 years of manufacturing, R&D, and market development experience. This includes development and commercialization of biomaterials, manufacturing technologies, recycling, and composites. Dan has led commercialization of a wide range of products and processes innovations including sustainable cellulosic materials and the application of AI in manufacturing. Dan joined Oak Ridge National Lab as Senior Staff, Leader of Industrial Collaborations in 2022. Together with his network of composite industry thought leaders, Dan identifies R&D needs to meet clean energy and decarbonization goals. Dan also develops the industry partnerships needed for ORNL researchers to address those needs.
​
​
Convergent Manufacturing of Composites: Integrating Advanced Processes for Productivity, Yield, and Performance
Thursday, May 22, 2025 | 11:00 am – 12:00 pm
​
The increasing complexity and performance demand in modern industries necessitate innovative manufacturing approaches that seamlessly integrate multiple techniques. Convergent manufacturing represents a novel paradigm by combining complementary advanced manufacturing processes such as additive manufacturing (AM), machining, compression molding, thermoforming, and tape layup to optimize material properties, functionalities, improve efficiency, and enable new design possibilities. Combining the strengths of multiple process technologies through convergent manufacturing strategies can increase productivity, reduce waste, increase yield, and expand the performance envelope of composite manufacturing.
Convergent manufacturing technologies include Additively Reinforced Thermoforming (ART), AM-integrated machining, and AM- compression and injection molding and hybrid composite molding. The ART process, developed by Oak Ridge National Laboratory, merges AM with thermoforming to create reinforced polymer sheets with tailored structural integrity and cost efficiency. Similarly, AM combined with machining enhances precision, surface finish, and mechanical properties, while AM-driven compression molding and tape layup techniques improve fiber alignment, load distribution, and manufacturability of complex geometries. By leveraging these hybrid techniques, manufacturers can reduce material waste, optimize structural performance, and accelerate production cycles across aerospace, automotive, and transportation industries. This presentation will examine key technical advancements, system integration challenges, and real-world applications of convergent manufacturing, demonstrating how these synergistic methods redefine the capabilities and efficiency of composite fabrication.